
The great thing is being able to pull out the individual pieces and check views across rooms, out windows, down hallways, and so on. Print each room/space including the entourage elements (couches, chairs, millwork, etc.) and then put the individual pieces of the model together to form an overall spatial model. Use the section box to cut the walls at a height just below the door thresholds, and cut the sides at the spatial parameter of rooms or spaces while working within the dimensional parameters of the build platform (for us 4×4″). The trick we have found that works great with extrusion printing, and really resonates with a client’s ability to understand and communicate about space/spatial configuration is to export a 3d model in a room by room, or space by space model of the design by: In Revit, open a 3d axonometric view and align the view to a section, or turn on the section box tool (in view properties). More to come on this topic soon – including a method of printing per room/space that we have gotten a big kick out of, that we think clients will really like.Ībsolutely – in fact, i just put it in my queue for a tutorial. Right now, they aren’t quite to the “design is done hit print and get your model” phase – but with MakerBot and Autodesk now officially collaborating, it is going to get there within the next couple of generations of hardware/software (again, my opinion). The main issue with the extrusion printers is figuring out how far you can push them in terms of thinness (mullions are particularly tricky), and the right way to work with gravity (building up from edges). Even thought it is an extra step, we like it. Revit to *.fbx to Max to *.stl has worked 100% of the time. Second, we have had a bit of inconsistency, again, nothing that probably couldn’t be resolved with finding the right work flow – but any minor inconsistency translated to 200+ students can create a real mess.
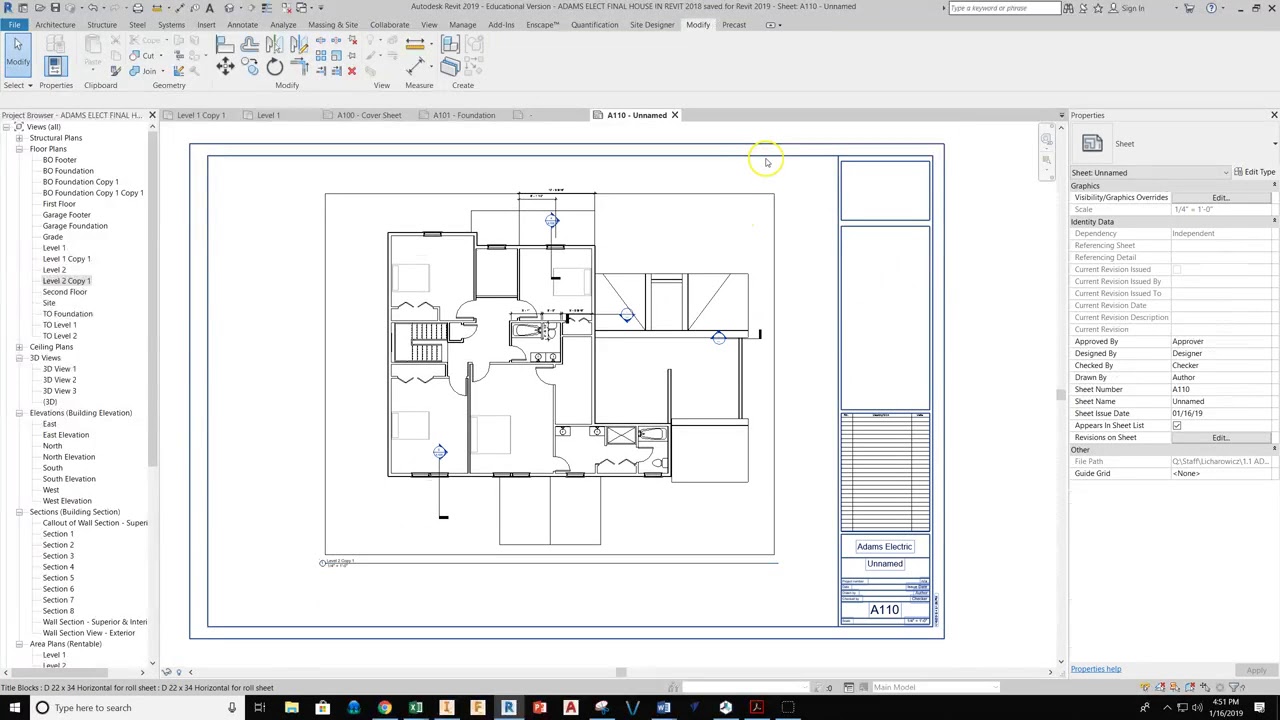
For instance, RepG is a 4″x4″x4″ work space – the initial import brings in an object at the building scale (hundreds of feet by hundres of feet) if exported directly from Revit. Since most projects coming from Revit need to be, say, a 1/16″, it is easier to accomplish this result in Max than RepG (my opinion). Scaling is difficult in ReplicatorG, and easy in 3ds Max. From business cards, banners, posters, boards, and books Del Mar Blue Print can offer what you need.We had two issues – first, we (Hammons School of Architecture) are an academic institution – so we are trying to funnel as many people through a comprehensive process as possible…in other words – what one process will work the best for the majority. We also offer many printing and digital services. Let us help you with your computer aided design needs. We are located in Del Mar, California, and have been in business for over 30 years. You can impress your client, by offering a 3D printed model.Ĭonvert2AutoCAD is owned by Del Mar Blue Print Co. We can print you a model home or commercial building quickly and accurately.
Revit print to scale pdf#
We specialize in PDF to DWG conversion for architects, engineers, and designers.īesides 2D CAD, we also offer BIM services like 3D modeling, 3D printing, and rendering. Our expert drafters can scale any file using AutoCAD scale factor charts.
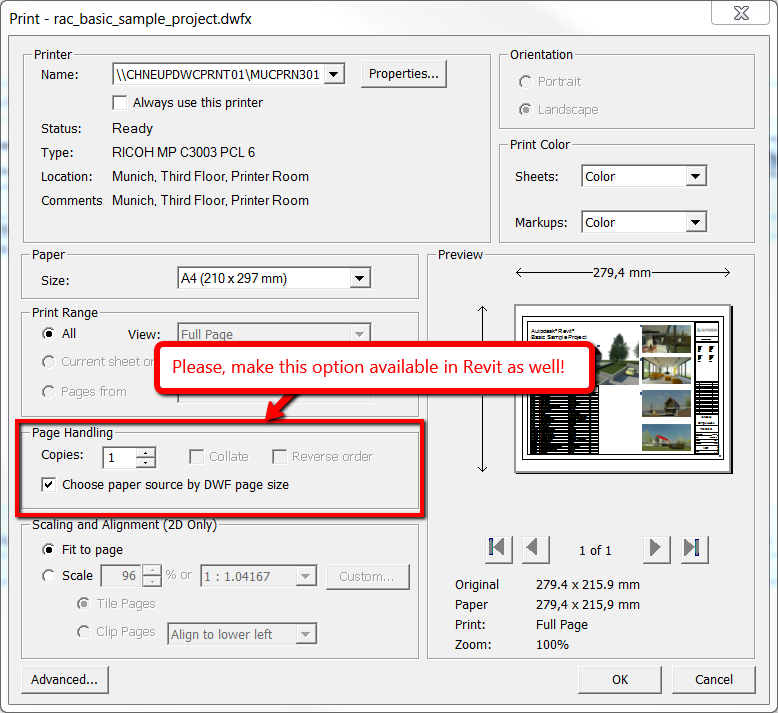
Our pricing is the lowest around, and will save you hours of time, and money.
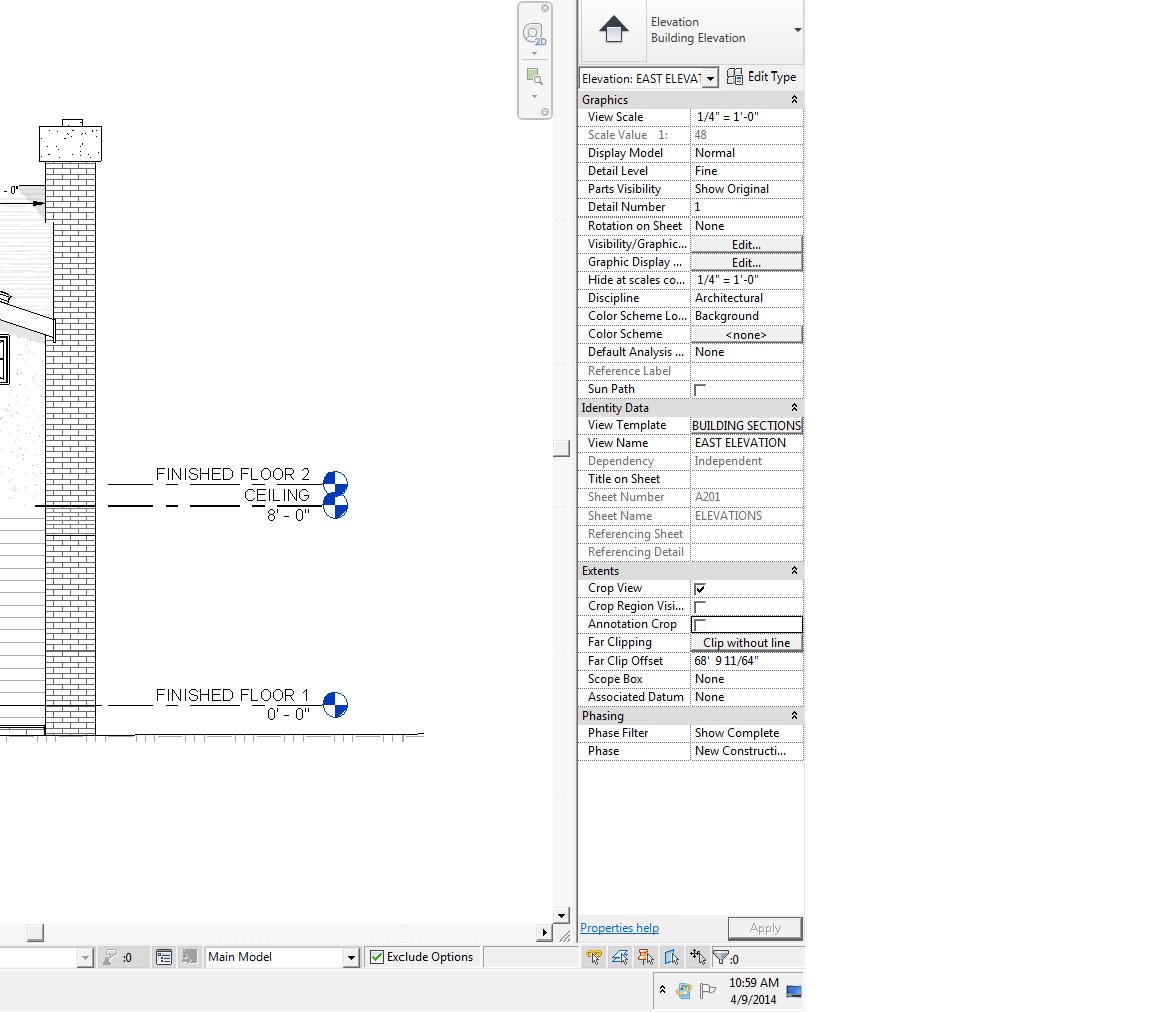
Hit the ground running on your next project. Converting to CAD is ideal for remodels, and to clean up hand-drawn plans. Our quality and turnaround is the best in the business. We get the AutoCAD file to you in as little as 24-hours. We can convert any type of architectural, structural, engineering, plumbing, electrical, landscape or any other plan to a DWG, PLT, or DFX file. Our AutoCAD service can save you time and money by offering the best and quickest result, so you can have time for your design.

offers conversions of your PDF, TIF, JPG, and other file types, to vector CAD files.
